- Home
- 制程工艺
制程工艺
聚鑫MIM
MIM典型加工流程
粉末冶金加工或金属注射成型(MIM)是学科跨界产物,将塑料注射成形技术引入粉末冶金领域的一种新型金属零部件近净成形加工技术。它结合了塑料注射成型的设计灵活性和锻造金属的强度与完整性,为复杂零件几何形状提供了成本效益的解决方案。MIM是粉末冶金和工业领域中发展迅猛的高新技术之一。MIM工艺通常包括混炼、成型、脱脂和烧结四个独特的加工步骤,用于生产最终零件。
1. 注射料的混合与制粒 将金属粉末与热塑性聚合物(通常称为粘结剂)在加热状态下进行混合,以确保每个金属颗粒表面均匀覆盖一层粘结剂。这样得到的混合物称为喂料。喂料冷却后,通过造粒机制备成几毫米大小的颗粒,作为注射成型机的注塑料。
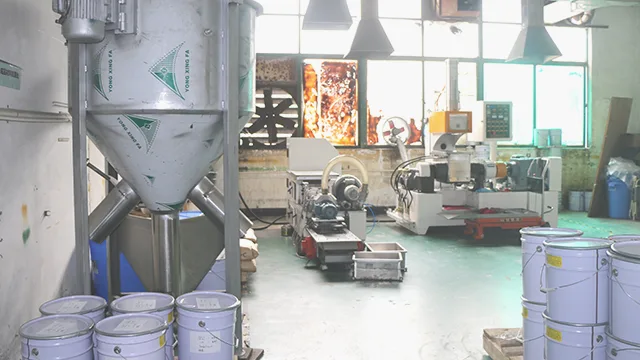
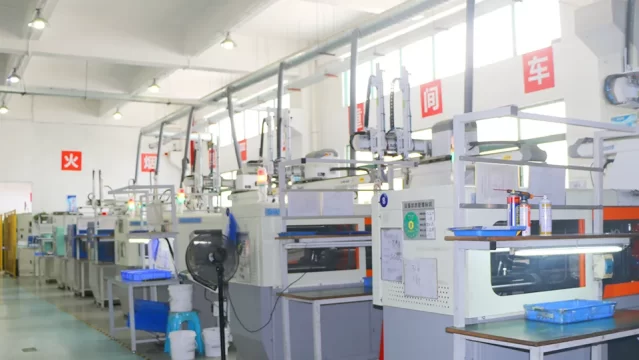
2. 注射成形 将喂料加热至熔化状态,并通过往复运动的螺杆将其强制喂入模具中的浇口。随后冷却,从模具中脱出成形的零件,获得生坯。
3. 脱脂
采用专用的脱脂设备对注射成形后的生坯进行处理,排除零件中约90%的粘结剂。剩余的10%残留粘结剂起到支撑作用,以便脱脂件进入下一道烧结工序。剩余的粘结剂将在烧结过程中的热脱阶段完全排除干净。
采用专用的脱脂设备对注射成形后的生坯进行处理,排除零件中约90%的粘结剂。剩余的10%残留粘结剂起到支撑作用,以便脱脂件进入下一道烧结工序。剩余的粘结剂将在烧结过程中的热脱阶段完全排除干净。
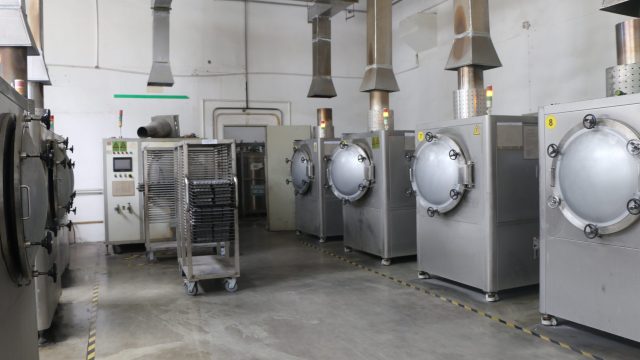
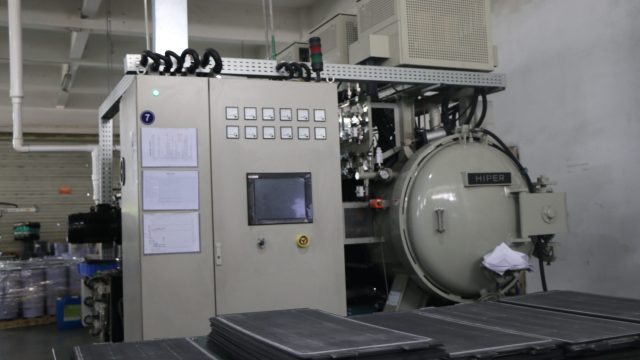
4. 烧结
将脱脂后的产品放置在陶瓷板上,然后放入烧结炉中。通过精确的温度控制, 逐渐将炉子温度提高至材料熔点的85%左右。烧结后的产品相对密度约为98%,其性能与通过棒材切削加工获得的零件相似。有时为了获得更精密的公差或增加材料性能,可以在烧结后进行整形、机加工、热处理及电镀等工艺。
将脱脂后的产品放置在陶瓷板上,然后放入烧结炉中。通过精确的温度控制, 逐渐将炉子温度提高至材料熔点的85%左右。烧结后的产品相对密度约为98%,其性能与通过棒材切削加工获得的零件相似。有时为了获得更精密的公差或增加材料性能,可以在烧结后进行整形、机加工、热处理及电镀等工艺。
聚鑫MIM
MIM的优势
01复杂的几何形状
MIM工艺通过类似于注塑模的模具进行成形,因此能够实现极高的几何形状设计自由度。只要注塑模具可以成形的产品,基本上都可以采用MIM工艺进行生产制造。
02优异的材料性能
MIM工艺通常在5-7天内完成生产周期,一旦一个周期结束,就可以持续供货。根据需求,日产量可以从几百到数十万不等,满足各种规模的生产需求。
03适合大批量生产
MIM产品具有高密度特性,使其具备卓越的材料性能,基本接近板材的性能水平。因此,MIM特别适用于对产品使用性能有特殊要求的零件。
04精致的外观
由于MIM原料粉末采用的是D90在18um以下的粉末,烧结坯的表面粗糙度可以达到约Ra0.8,这为后续的打磨、抛光、电镀等处理提供了便利条件。
05材料多样性
目前已经证明几乎所有的材料都可以通过MIM工艺进行生产,但最好选择不锈钢材料进行生产,以获得最佳效果。
06尺寸精度高
粉末注射成形的尺寸精度一般在+/-0.5%左右,特殊情况下可以实现+/-0.3%的尺寸精度。
聚鑫MIM
工艺对比
比较项目 | 金属注射成型(MIM) | 精密铸造 | 机加工 | 钣金冲压 |
---|---|---|---|---|
密度 | 98% | 98% | 100% | 100% |
拉伸强度 | 高 | 高 | 高 | 高 |
表面光洁度 | 高 | 中 | 高 | 高 |
微小化能力 | 高 | 低 | 中 | 高 |
薄壁能力 | 高 | 中 | 低 | 高 |
复杂程度 | 高 | 中 | 高 | 低 |
设计宽容度 | 高 | 中 | 中 | 低 |
生产能力 | 高 | 中 | 中-高 | 中 |
材质范围 | 高 | 中-高 | 高 | 中 |
供货能力 | 高 | 中 | 低 | 高 |
相较于其他的金属成形方式,MIM工艺的优势具体体现如下
优势 | 具体表现 |
---|---|
极高的设计自由度 | MIM工艺能够像塑胶注塑成形一样将复杂的金属零件直接成形,允许三维形状的自由设计,理论上塑胶可以实现的结构都可通过MIM工艺实现。 |
出色的理化性能 | MIM产品组织均匀、致密度好,烧结密度可达到理论密度的98%以上,甚至接近于理论密度,其理化性能表现非常出色,产品强度、硬度、延伸率等力学性能超过传统工艺。 |
更高的尺寸精度 | MIM产品一次成形尺寸精度可达+/—0.3%,一般精度要求的产品无需后加工:如配合其他加工方式,可以获得更高的尺寸精度。 |
更多的材料选择 | MIM工艺几乎可使用绝大部分金属材料,特别适用于对材料性能较高的应用场景。考虑到经济性,主要的应用材料涵盖铁基、镍基、铜基、钛基金属或合金。 |
精致的外观表现 | MIM工艺的烧结坯表面粗糙度(Ra)可做到1μm,更可以通过各种表面处理方式获得炫目的外观效果。 |
灵活的量产能力 | MIM工艺可以灵活调整和迅速提升产量,从每天几百件到每天数十万件都可以快速响应。 |
极高的原料利用率 | MIM 工艺原料利用率接近100%,是一种近净成形技术,可有效避免材料的浪费。 |
显著的批量成本优势 | MIM工艺近净成形,相较于其他工艺,特别是结构复杂产品,利用MIM 工艺批量生产成本优势明显。 |
聚鑫快速响应您的需求,提供24/7免费技术咨询
3小时极速获取报价